ESI Robotics has finished another successful project: this time, we produced a squaring machine for Globale RC. The company challenged us to develop a squaring machine that would automate the adjustment of part measurements. ESI Robotics embraced this challenge and, in the end, the project was a success!

Globale RC experienced an increase in demand for its products, which forced them to meet the market and increase its production. To do this, they identified the need for a frame-making machine.
By acquiring this machine, they aimed to increase production and be more efficient in assembly, since they had many manual processes, which ended up slowing down production.
As well as increasing production, the equipment developed by ESI Robotics has enabled Globale to improve planning and organization on the factory floor, as they can dedicate this machine to the manufacture of standard products, which can be produced in series.
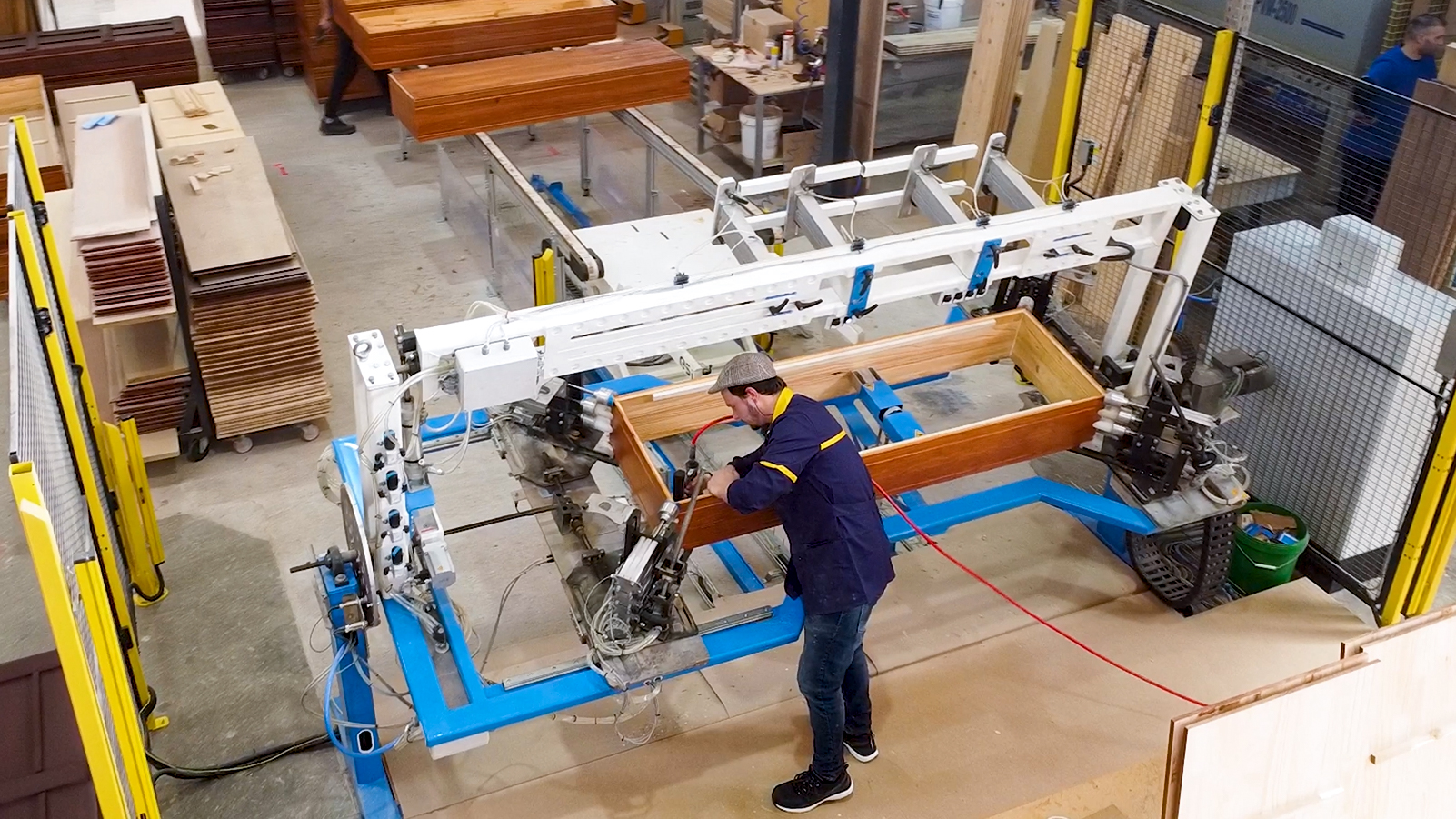
How the Squaring Machine Works
The Urn Framing Machine is designed to adjust to the measurements required for the production of various references for urn lids and boxes. The operator places the pieces needed to produce these references, and the machine makes the frames between them.
The cell is divided into two systems: the squaring machine, used by the operator to produce the ballot box boxes and lids; and the extraction system, which consists of a mobile lifting table (extraction device) and a conveyor, responsible for extracting the finished products.
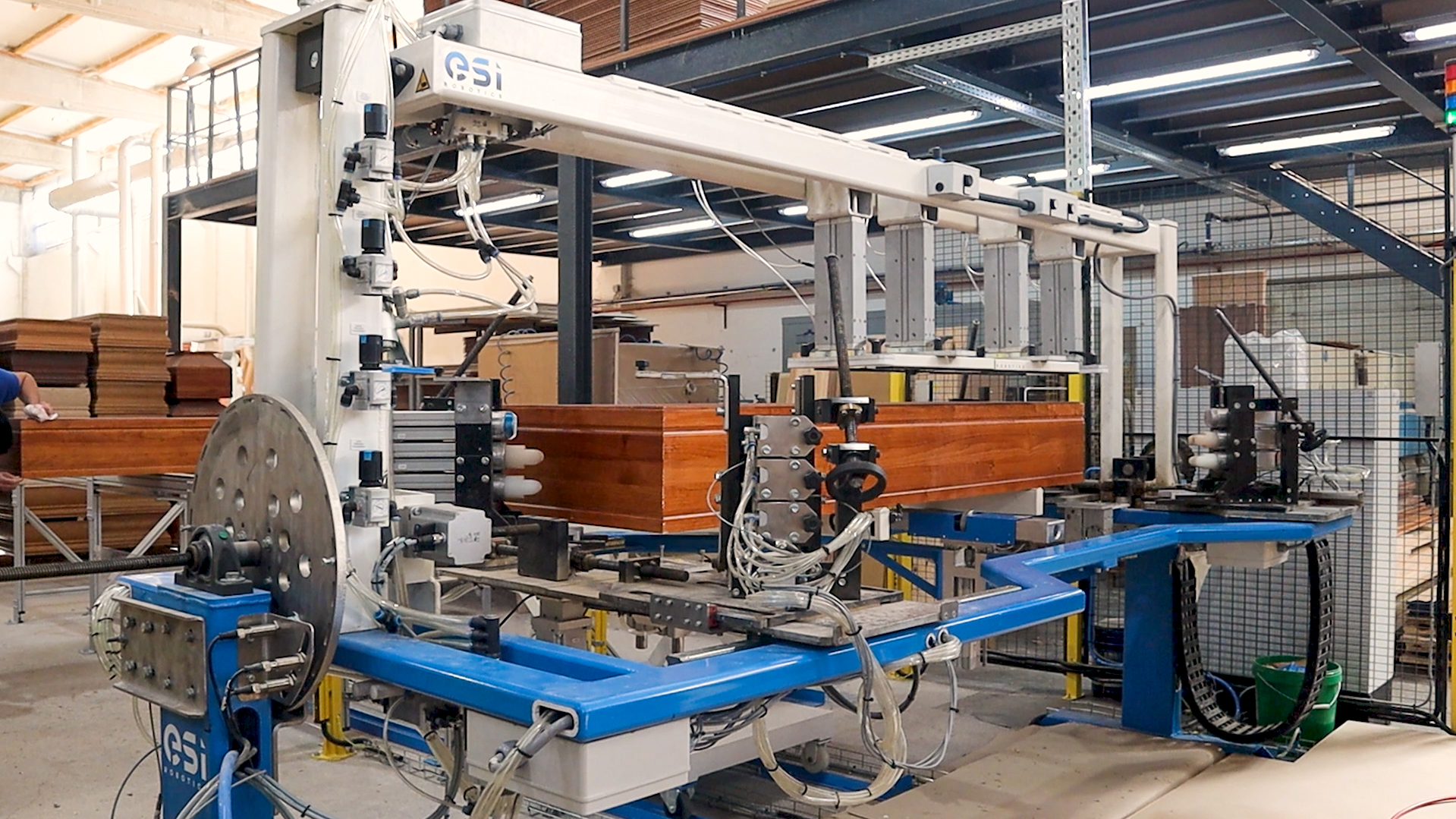
The machine is based on standard manual adjustment equipment, but its main feature is that all length and width adjustments are provided by stepper motors. ESI Robotics has integrated software and created an interface console so that the operator can choose the bottom and lid measurements and the machine makes the adjustments automatically. This frees up the operator to focus on material preparation.
Project Results
For Tiago Rebelo, executive manager of Globale RC, one of the positive points of working with ESI Robotics was being able to follow the machine's entire production process. As with all projects, at ESI Robotics we like to follow up very closely with the customer, so that they know exactly what they are buying and our technical solution can be adapted and optimized to their specific needs.
This project was completed, ESI was able to meet the customer's needs and double production capacity. In terms of environmental impact, the machine has an impact on reducing wood waste, since, with the equipment tuned to Globale RC's production needs, the likelihood of producing a non-compliant product is greatly reduced.
"I found their portfolio and the other projects they had already done very interesting. From there we started to think, we also must invest in our own engineering, in Portuguese engineering. We'd never done that, it was a long shot for us, because we're not used to it. Everything we did was with Italians, Germans, and Austrians; So, we thought, " okay, we'll invest in ESI”.
Tiago Rebelo, Executive Manager of Globale RC
SEE ALSO: Innovation in the Plastic Industry: Discover our Case Studies
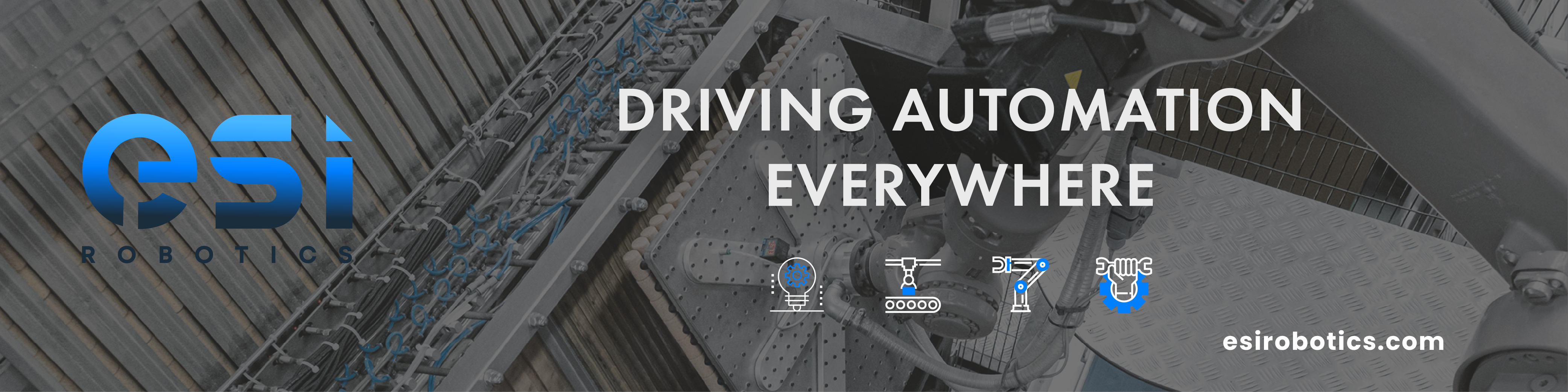